JOIN A FAMILY
OF INNOVATORS
CAREERS AT INTRIPLEX
Build a rewarding career and be part of a group of talented individuals that provide reliable, high-quality, and innovative stamped components that make an industry impact.
At IntriPlex, our employees are our most valuable appreciating assets. We understand that the success of our business today and tomorrow rests squarely with our people. We do our very best to attract, develop, and retain outstanding human resources. The result is a culture of precision that is developed and nurtured at our core.
The IntriPlex Approach
Our 35+ years of success comes from hiring the right person the first time. We remain committed to finding and retaining leaders and team members who have both the desire and talent to live and breathe the “exactness” that resonates in our team. Our employees are fully engaged in improving our products and processes, and the mission is clear—we are dedicated to bringing innovative and enabling precision component solutions to our customers so that their products can meet and exceed the expectations of their customers. We remain diligent in our commitment to superior world-class quality and customer service. We want everything that we do and every point of contact to reflect that.
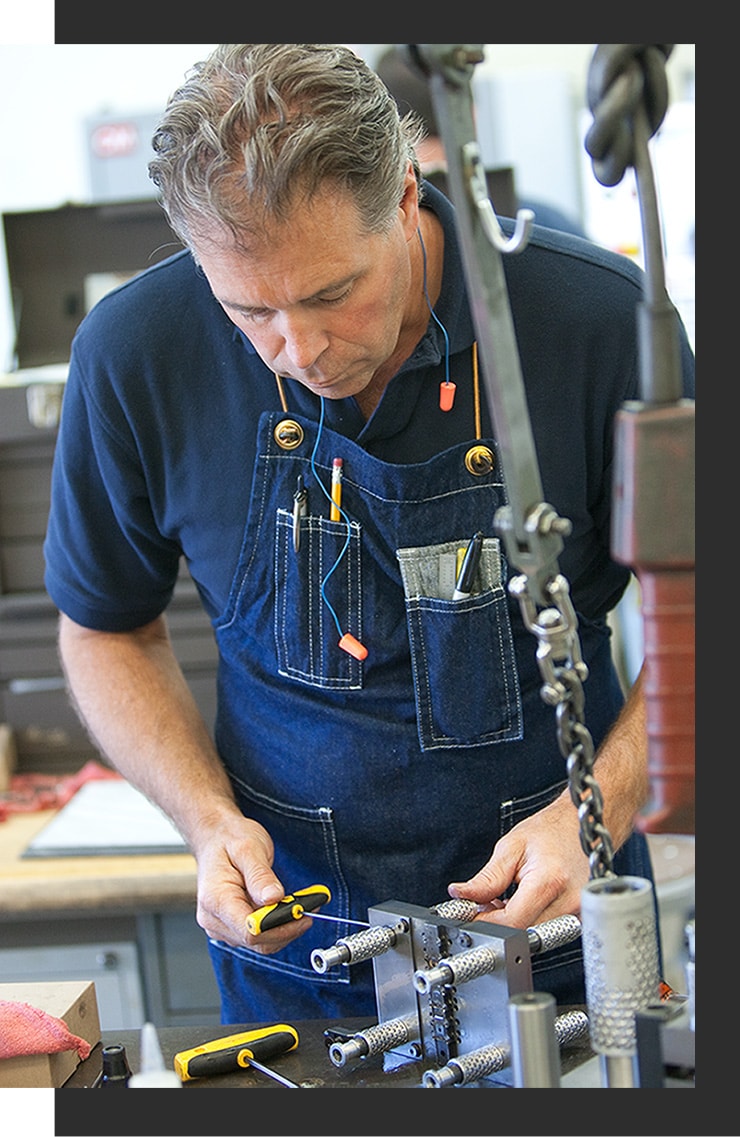
OUR FAVORITE REASONS TO WORK AT INTRIPLEX
An atmosphere of respect
IntriPlex fosters a professional yet “family style” work environment where everyone is treated with dignity and respect. Our people genuinely care about the well-being of our customers and of one another.
Creativity in Diversity
IntriPlex is very proud of the diversity in our organization. This diversity in the background, experience, and culture of our people provides multiple viewpoints that form fertile ground for creativity.
Continuous learning
Curiosity is our compass. Our commitment to accomplishing incredible things emboldens us to tackle big challenges. Experience autonomy in your career with new opportunities and complex problems to support individual development.
Comprehensive benefits
Medical, Dental, & Vision Insurance
Life and AD&D Insurance
401-K with Company Match
Competitive Salary with Performance Compensation
Section 125 FSA Account
At IntriPlex, we approach our work with the same integrity and passion as we do each product we create. We believe that our success is made by our dedicated team who believes in our mission to deliver the highest quality service and product. We want our employees to have fulfilling careers driven by curiosity and commitment. The challenges we solve are serious, but we have fun every day because we love what we do.
OPEN POSITIONS
Job Title: Tool & Die Maker
Department: Manufacturing
Reports To: Program Manager, Stamping Technology
Hours: 6:30 am – 3:00 pm, M-F
Pay Scale: $40 – $50 per hour, depending on experience
SUMMARY
The Tool & Die Maker will perform maintenance, trials, and troubleshoot complex stamp and dies. The position is a key part of a close-working manufacturing and engineering group that supports our internal and external customers and the operations of the company.
ESSENTIAL DUTIES AND RESPONSIBILITIES
As follows. Other duties may be assigned.
- Requires general knowledge of construction and maintenance of progressive metal stamping dies and ability to actively engage in new product/part development.
- Sets up and operates all basic machine tools, mills, lathes, grinders, and machinist hand tools.
- Capability to grind die components to +/-.0001” tolerance on tool steel and carbide is strongly preferred.
- Knowledge of shop inspection procedures, mechanical, optical, and computer-assisted measuring equipment.
- Understanding of SPC manufacturing environment.
- Analyzes and interprets specifications, including blueprints, engineering sketches, and verbal information.
- Requires general knowledge of various tool steels and their application.
- General knowledge of jigs and fixtures, automated machinery, and basic shop machine maintenance.
- This job requires the ability to work in multiple locations and/or to relocate to a different state.
SUPERVISORY RESPONSIBILITIES
None
QUALIFICATIONS
To perform this job successfully, an individual must be able to perform each essential duty satisfactorily. The requirements listed below are representative of the knowledge, skill, and/or ability required. Reasonable accommodations may be made for individuals with disabilities to perform essential functions.
- Language Skills: Ability to read, analyze and interpret scientific and technical journals. Ability to respond to common inquiries.
- Math Skills: Strong math skills, and problem-solving ability necessary.
- Reasoning Ability: Analytical skills necessary to maintain and troubleshoot precision, high-speed progressive dies.
- Physical Demands: Proper lifting techniques are required. Extended periods of standing may be required. Ability to lift up to 50 lbs on occasion.
- Work Environment: May require occasional exposure to the manufacturing areas where certain areas may require the use of personal protective equipment such as safety glasses with side shields, and mandatory hearing protection. For the most part, room temperatures are ambient lighting with traditional office equipment.
EDUCATION/EXPERIENCE
- Two years of technical school, and ten years of experience in tool and die making specifically progressive tooling. Previous involvement with new product development activities including tooling and process advancement working closely with tool designers preferred. Managerial experience is considered a plus.
IntriPlex Technologies is a global leader in high volume, precision metal stamping and forming technology, well-recognized for engineering excellence, product quality, and a broad product innovation portfolio across multiple industries. Today, IntriPlex places a growing focus on advancing battery technology with critical breakthrough stamping solutions for prismatic and cylindrical battery cell components. Our customers choose us to partner with them for innovative precision metal stamping solutions. We’re headquartered in Santa Barbara, California. We manufacture in the USA and Thailand.